Recyclers Focus on Sustainability and Regulatory Challenges of Low U.S. Recycling Rates
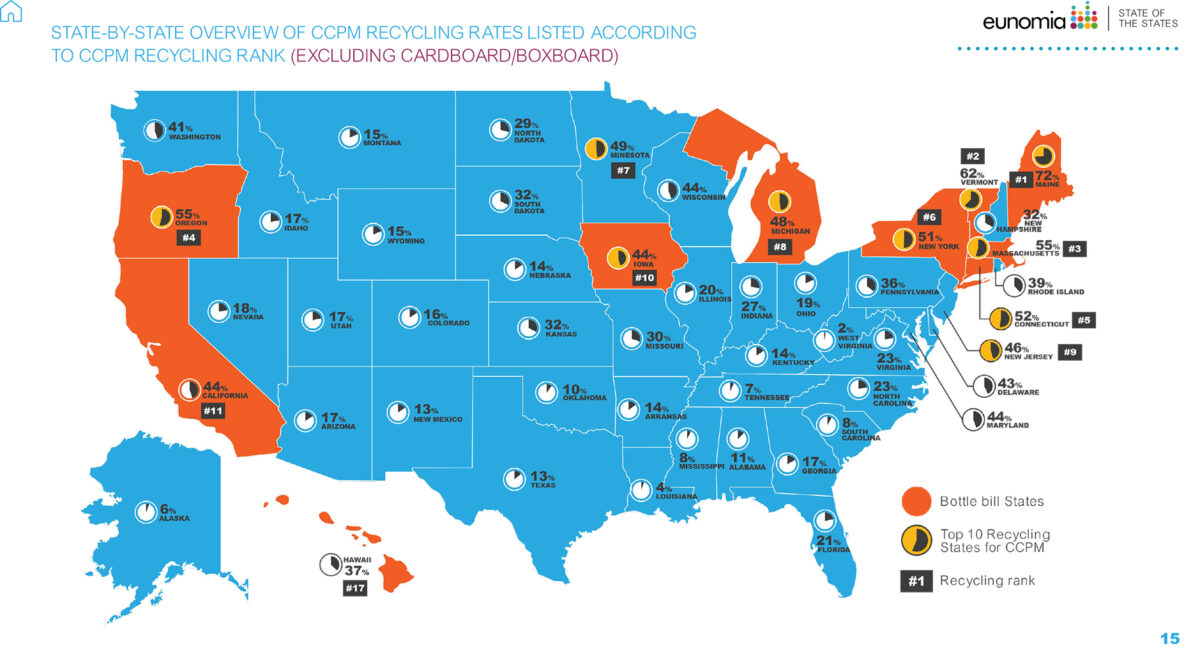
Industry confronts ‘green’ obstacles at annual APR conference
2,700 attendees were at the Association of Plastic Recyclers’ (APR) Plastics Recycling Conference in March, at the Gaylord National Harbor Hotel outside Washington, D.C.
Among the presenters, consultant Tonya Randell of Stina Inc., Sonoma, Calif., discussed film and bag recycling, including material quality, volumes collected and consumer access to recycling.
PE Films Are Recyclable but Mostly Landfilled
She revealed that most PE films are recoverable and compatible with the 17,000 film drop-off locations in the U.S. Her study used data from 15 of the largest materials recovery facilities (MRFs) representing 27 percent of California’s MRF capacity, yet only one site in the state formally accepts films. The entire MRF capacity in the Golden State collects approximately 260 million pounds of PE film, most of which is landfilled. Even though the data showed that ~65 percent of California residents had access to drop-off locations, the path of least resistance remains disposal, not recycling.
Rigid plastic fares better than flexibles in recovery and recycling, but the U.S. recycling rate has declined 5.7 percent since 2019 due to a combination of factors according to APR: stagnation in collection systems; lack of long-term contracts between buyers and sellers of recycled materials; proliferation of polymer types and packaging styles; and a patchwork of municipal, state and federal regulations.
There are over 9,000 recycling programs in the U.S. Harmonization of collection and sortation should be easier with rigid materials because 80 percent are PP, HDPE and PET. Roughly 20 percent is recycled, though there is capacity to recycle 40 percent.
“Consumer packaged goods companies are their own raw material suppliers,” said Steve Alexander, president of APR. The implication, therefore, is that it behooves these large multinationals to design packaging that is easy and economical to recover and recycle. APR offers design guidelines, certification programs and training programs to help companies streamline their packaging for recycling.
Andrew Brown, head of plastics and recycling at consultancy Wood Mackenzie presented information on PET dynamics: 27 million tons of PET resin are used for packaging and 36 million tons for polyester fiber. Brown showed that 14 kilotons (kT) of new recycled PET (rPET) capacity needs to come online before global commitments are met. Yet only 3 kT of new capacity is expected to come online by 2025.
EPR Could Boost Collection and Recycling Rates
A combination of extended producer responsibility (EPR) programs and new sortation technologies could contribute up to 10 percent more collection, but imports of PET flake will continue to arrive from Asia. Emily Friedman of ICIS, in Houston, stated that increasing rPET capacity in Asia is premised on getting certifications to export material to North American and European markets where a premium will be paid based on sustainability initiatives.
There is a limit to how much companies will pay for recycled materials, however, as evidenced by continued growth in virgin resin shipments and wide regional disparities in pricing between virgin and recycled materials. Friedman said markets and polymers are not homogenous, illustrating differences between HDPE (where virgin pricing is essentially decoupled from recycled) and PET (where virgin and recycled materials follow related price patterns).
In one panel discussion, Waste Management (WM), Dow and Natura PCR speakers presented successes and challenges in material recovery and reprocessing. The companies focused their remarks on films and flexibles, the fastest-growing segments for PE resins, which are becoming more visible in stores and in the environment. Low bulk density and contamination mean that PE film recovery requires continued investment in R&D and technologies to make recycling more efficient and cost-effective.
There are thousands of PE specialty films for specific needs that arrive commingled at recyclers’ facilities and must be homogenized. Dow continues to develop a pipeline of solutions as seen in its REVOLOOP product range. Like other APR members, Dow and Natura PCR complain about a lack of material—not surprising when tipping fees are low and there is little regulatory incentive to recycle. This explains why the U.S. film recycling rate is 2 percent.
Mining Waste for Recyclable Plastics
On the other hand, WM and Republic Waste Services announced significant investments in plastics recycling. The big news at the 2022 APR conference was Republic’s announcement of a $1 billion investment in a polymer research center in Nevada, where the company will mine its own waste for PET, PE and PP. The project is reportedly the first vertically integrated plastics recycling facility with an annual nameplate capacity of 100 million pounds of recovered resin. The core technology is a washing module from Krones of Germany that will generate clean washed flakes or pellets.
Republic also announced plans for a second polymer research center in the Midwest.
Natura PCR uses extrusion, filtration, optical sorting and devolitizing technologies in its factories, which will have a projected nameplate capacity of 300 million pounds in the next 18 months.
Up to 70 kT of recycling capacity will come online this year, when Dow’s collaboration with French company Valoregen goes online. This project combines elements of mechanical and advanced recycling processes in a single site to enable higher yields and reduce emissions by limiting the transportation of materials. Dow will be the primary off-take user of PCR (post-consumer recyclate) from the location.
The value chain for recycled plastics starts with collection and sortation, two phases that present different challenges. Speakers said materials are being collected, but are not making it to sortation, especially films. Collection technologies (mainly trucks) are not complicated but sortation technologies are. They are also expensive, contributing to the economic challenges of recycling lightweight, low-value materials.
Flexible Films Impact Economics of Recycling
Republic has purchased 17 near-infrared optical scanners to identify and separate PET and polyolefins, but they are not ready to focus on flexibles. Mike Centers of California-based Titus Recycling shared war stories about setting up secondary MRFs and how important they can be for difficult-to-manage materials, especially flexible films. The average throughput at a primary MRF is 50 tons per hour but only 8 to 13 tons per hour at a secondary MRF, underscoring the poor economics of flexibles recycling.
Data from Eunomia and other sources reveal that American states with deposit schemes report an average recycling rate of just over 50 percent. The value of presorting mainly PET bottles is evident, with premium prices paid for clean, A-grade bales which are easily converted into higher-grade flake or pellets, and ultimately preforms or extruded sheet. There appears to be tension between curbside recycling programs and deposit programs: more bottles sent to deposit programs mean fewer bottles for curbside collection, thus reducing the value of that stream.
Consumer ‘Despair’ Over Collection
Suzanne Shelton of the Shelton Group delivered her latest data on the American consumer’s perception of plastics recycling. With 17 years of trending data in three large polling data sets, Shelton reports that 76 percent of the U.S. public say recycling makes them feel better about their consumption, but recent responses indicate that they are starting to doubt whether recycling is living up to its promise. “Measurable doubt” has increased 50 percent since 2016.
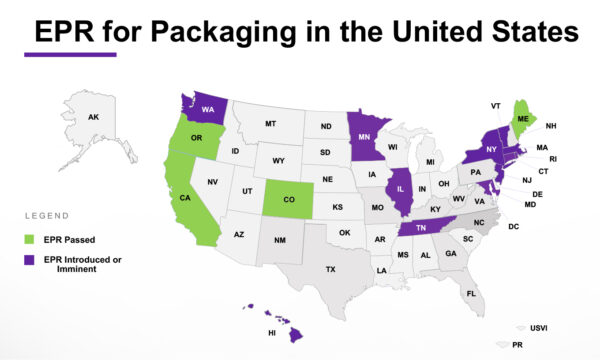
Extended Producer Responsibility programs are law in four states and under consideration or imminent in 11 more. Courtesy of American Beverage
People are becoming uncomfortable with the gap between self-identification as “eco-aware” and the actual, measurable impact of their choices. “This is an emotional issue that will not be resolved by the presentation of facts and data,” stated Shelton, something that will likely perplex the rational engineering crowd. Little wonder then that 59 percent of the consuming public believes companies should bear some responsibility for end-of-life management of materials and products they produce in such massive quantities.
Moderated by Keefe Harrison of The Recycling Partnership, a panel featuring speakers from The Ocean Foundation, APR, Virginia Tech and the Plastics Industry Association offered perspectives on the consumer question.
Addressing the “sense of despair” consumers feel about low recycling rates, Steve Alexander of APR called out marketers for ignoring end-of-life concerns in favor of increasing sales. Framing circularity as “garbage in, garbage out,” the recycling industry cannot be responsible for cleaning up the bad decisions of others in the value chain, he said.
Jennifer Russell, assistant professor at Virginia Tech, stated that trust has been eroded with customers on multiple fronts, including a proliferation of signage on packages related to the ability (or not) to recycle and industry’s consistent resistance to policy changes, e.g., EPR and deposit systems.
The Recycling Partnership said it would cost $17 billion in capital expenditure to “fix” the recycling system, yet APR’s Alexander was characteristically blunt about how that investment should be made. “The last thing we need is government investment [in the form of grants] because they are typically one-and-done,” which does not change the spot-market nature of recycling markets as they exist today. Long-term contracts are required to secure and sustain material supply. This also would send a stronger signal to private investors who repeatedly state that the lack of steady and stable supply chains leads to such price volatility that they cannot model returns with enough confidence to approve large investments.