Optimizing Pearlescent Pigment Dispersion
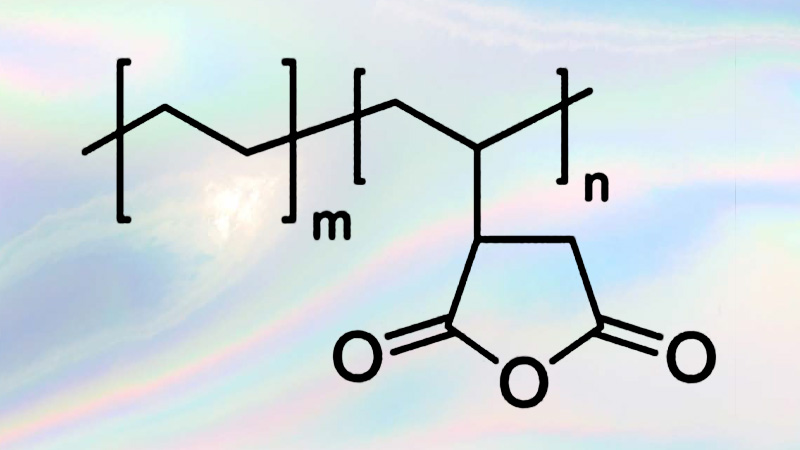
Clariant data highlight advantages of metallocene PE waxes on pearlescent aesthetics
Pearlescent pigments are a popular color option. Among the suppliers of process aids for these materials is Clariant Corp., whose fine-grain Licocene maleic anhydride (MAH)-grafted metallocene polyethylene waxes are formulated for various process benefits. In this analysis of two grades, PE MA 4221, described as a mold release forpolyester and polyamide resins that doesn’t affect the initial color of compounds, and PE MA 4351, a compatibilizer and dispersing aid for reinforced plastics, Clariant researchers compare the performance of these materials to others on the market. Their paper is titled “Maintenance of Particle Size and Improved Wetting-out of Pearlescent Pigments in Masterbatches with Clariant’s Functionalized Metallocene Polymers.” Following is the abstract and data.
Abstract: Pearlescent pigments provide a special, sparkling, visual effect, which is seen as luxurious and more finished than non-reflective pigments in articles such as bottles, cosmetics cases, vases and automotive components. However, these special effects pigments are often challenging to process consistently and economically as they can be difficult to wet out, which causes clumping, thus limiting process efficiency, the intended aesthetic effect and ultimately, the physical integrity of finished articles.
In an effort to properly disperse these pigments and still attain the desired effect (read particle size and color match), many masterbatchers and compounders add an excess of the pigments and easily volatile dispersants, then inadvertently impart excess shear with high rpm and aggressive screw designs. Another common practice is to oversize the pigment (pearlescents come in various flake sizes) before compounding, with the goal of hitting the target particle size needed to maintain desired appearance. These techniques often result in lot-to-lot inconsistency, reduced economics and reductions of the desired surface gloss of finished articles, due to exusion of the dispersants, haze and reduced pearlescent particle size.
Clariant’s Advanced Surface Solutions Team has developed MAH-grafted metallocene polymers, namely Licocenes PE MA 4221 and PE MA 4351, which improve dispersion, reduce shear and extrusion pressures, and increase output rates without dulling the surface. These achievements are explained and quantified here, via filter pressure value (FPV) testing, decreased speck counts (film analyses), and increased color and gloss development. This is possible from the following inherent traits of the Licocene metallocenes:
- High strand/tensile melt strength due to high molecular weight when compared with common olefin dispersants
- High percentages of MAH grafting and
- Narrow molecular weight distribution courtesy of the metallocene catalyst used to control their syntheses.
Typical PE-MAH Functional Structure:
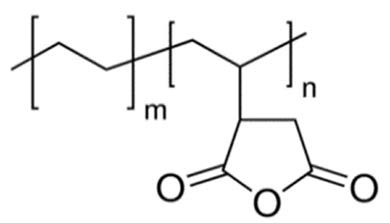
Note: Licocene PE MA 4221 has 1.5 percent nominal MAH grafting. Licocene PE MA 4351 has 6.0 percent nominal MAH grafting.
Dispersant Evaluations
To confirm the efficacy of the Licocene grades, masterbatches were made with 30 percent total pigment content (25 percent pearlescent + 5 percent PR 122 in linear-low-density PE) on a Jieya CET-20 x 42D twin screw extruder at typical LLDPE processing temperatures (170 to 190°C) after cold mixing the batches at low intensity in a Henschel mixer. Between 5 and 15 percent of various waxes were tested for efficacy in the masterbatches.
The masterbatch formulations are listed in the chart below
Masterbatch Formulae
Ingredient | 1# | 2# | 3# | 4# | 5# | 6# | 7# | 8# |
---|---|---|---|---|---|---|---|---|
LLDPE 6101 | 0 | 55 | 55 | 55 | 55 | 55 | 60 | 65 |
Kuncai KC 120 (Pearlescent) | 25 | 25 | 25 | 25 | 25 | 25 | 25 | 25 |
PR 122 (Clariant, 1102B) | 5 | 5 | 5 | 5 | 5 | 5 | 5 | 5 |
Licocene PE MA 4221 | – | 5 | 10 | 15 | – | – | – | – |
Licowax PE 520 | 15 | 10 | 5 | – | – | – | – | – |
Competitor PE Wax * | – | – | – | – | 15 | – | – | – |
Competitor PE MAH Wax * | – | – | – | – | – | 15 | – | – |
Licocene PE MA 4351 | – | – | – | – | – | – | 10 | 5 |
* Competitive waxes were advertised as offsets to PE 520 and PE MA 4221 respectively.
All of the masterbatches were then let down into base polymer to yield the following total pigment concentrations for testing.
- Filter Pressure Value Test: (2.5 percent pigment, PZ 25)—16.67g masterbatch into 183.33g base polymer LDPE 955 from Hanwha (MFI = 7).
- Film Testing: (1 percent pigment concentration, 80μm thickness)—16.67g masterbatch into 483.33g of film grade LDPE (MFI 0.75) from LyondellBasell.
- Gloss Measurement: HDPE J44-20 (MFI 20) from Sinopec to let down 1g masterbatch into 99g base polymer (0.3 percent pigment concentration) via single screw extruder into a granulate. Then, injection molded plaques to measure gloss at 60°.
Filter Pressure Value Test
8.3 percent of each masterbatch (2.5 percent pigment loading) yielded the following results.
Observations:
15 percent Licocene PE MA 4221 showed the best dispersion (i.e., lowest FPV) in an LLDPE carrier.
10 percent Licocene PE MA 4351 (higher MAH content) can achieve similar dispersion to PE MA 4221.
All MAH-grafted waxes outperformed standard PE waxes for reducing FPV results in this test.
Discussion:
The low FPV results for the maleated Licocenes support the theory that the maleated ends have a higher affinity for the surface of a pearlescent—i.e., metal oxide coating (usually TiO2) and possible metal hydroxide sites on the pearlescent (mica or potassium aluminum silicate)—than non-maleated PEs, thus adhering to the surface and separating the pigment particles, then assisting their flow, incorporation and compatibility in the PE matrix while stabilizing them from re-agglomeration. Also, any maleic acid formed from residual moisture will have strong bonding effects with free aluminum from sheared parts of the pearlescent pigment exposing aluminum. The slightly better results for 15 percent PE MA 4221 versus 10 percent PE MA 4351 may be simply attributed to the higher dosage of PE MA 4221, allowing greater distribution—and hence more opportunities for MAH interaction—within the polymer melt.
Blown Film Defect Testing
Following are results with 15 percent total pigment (3.33 percent masterbatch into base polymer).
Observations:
Licocene PE MA 4221 showed the fewest and smallest specks, thus optimum dispersion.
Licocene PE MA 4221+Licowax PE 520 blending at 1:2 achieves a balance between performance and formulation cost. Licocene PE MA 4351 (with higher MAH content) achieves similar dispersion to the PE MA 4221 at a lower dosage (5 to 10 percent), thus achieving similar cost and performance.
Discussion:
The 15 percent loaded version of Licocene PE MA 4221 again demonstrated high dispersion and reduction of re-agglomerated pearlescent pigment. Some economy was seen, along with the next best results with a 1:2 mixture of Licowax PE 520 and Licocene PE MA 4221. This may be a consequence of the particular screw type or mixing elements in the film extruder.
Gloss Comparison
Analysis of 1g masterbatch into 99g base polymer, which equals 0.3 percent pigment.
Observations:
Licocene PE MA 4221 (15 percent in masterbatch) and a competitive MAH-grafted grade at the same dose showed the most gloss, which is typically desired in pearlescent packaging and parts. Licocene PE MA 4351 (10 percent in masterbatch) and Licowax PE 520 (15 percent in masterbatch) showed the next best gloss results. Reducing the MAH-grafted waxes below 10 percent generally results in a major gloss reduction.
Discussion:
Gloss on the surface of a color plaque (at 60°) may be affected by exusions or blooming of additives (less is usually better) on resinrichness at the surface. The data suggest that the flow would be more laminar with optimally wetted-out pigments, and the reduced pressures and lubricating effects of the waxes. These effects should make for a less turbulent flow, meaning that the pearlescent pigments would lay flat and reflect more. The high molecular weight of the polymer waxes reduces blooming or hazing, while the maleated ends are more likely to keep the polymer ends anchored to the pearlescent pigments, thus leaving the aliphatic parts of the waxes to help compatibilize the PE matrix side on the metal surfaces. The index of refraction of the PE moiety is also the same as the plaques (or clients’ parts), thus reducing haze, which can reduce gloss.
Screw Cleaning and Purging
Pearlescent pigments are reportedly sticky when not wetted out properly. Extrusion operators often complain about the long purging time required, and the difficulty in pulling extruder screws to clean. When using the MAH-grafted Licocene PE MA 4221 and/or 4351 grades, the extruders reportedly cleaned easily, without caking of pigments on the screws. (See pictures of pigment-caked screw and clean screw.)
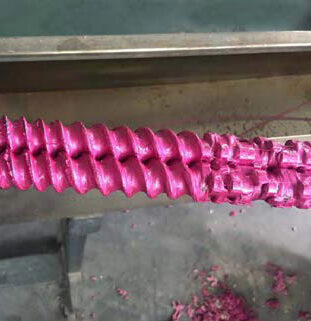
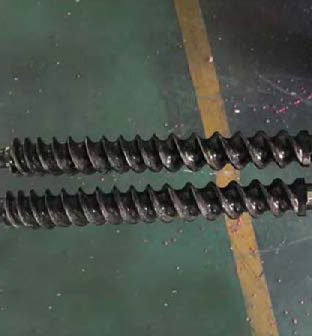
Summary: The dispersion benefits demonstrated in this study—namely fewer agglomerates (specks) in the film study, lower filter pressure values and higher gloss when using an optimized dosage of the properly formulated MAH-grafted Licocene grade suggest that the integrity and appearances of finished products will benefit from their use, by showing less breakage, improved impact resistance and improved appearance. This reduces the need to use excessive shear when compounding, which diminishes the particle size of pearlescent and metallic pigments, reducing their visual impact.
The improved dispersion and consistency achievable should also allow a reduction of pearlescent pigment concentration while achieving the same effect, which will help reduce cost. Also, as polymer flows easily with better pigment wetting, less torque and shear mean that gentler screw designs may be used, which would further enhance the results. As this application has the same basic conditions and demands as metallic pigment dispersion and maintenance of particle size for optimal sparkle, the same results should be expected for metal.
The low odor of the metallocene Licocene PE MA grades versus competitors (due to their manufacturing process leaving almost no free maleic anhydride or maleic acids) also suggests that organoleptic results should improve in cosmetics and personal care items, which often rely on pearlescent pigments for their aesthetics.
This article was reviewed and edited by Plastics Engineering. For more information, contact Clariant Additives: In Asia-Megan Mao, regional technical manager ([email protected]); Europe and MEA-Christian Lechner, global technical manager ([email protected]); India and South Pacific-Souvik Sengupta, regional technical manager ([email protected]); Americas-Frank Neuber, regional technical manager ([email protected])