Interest Grows in Chemical Recycling
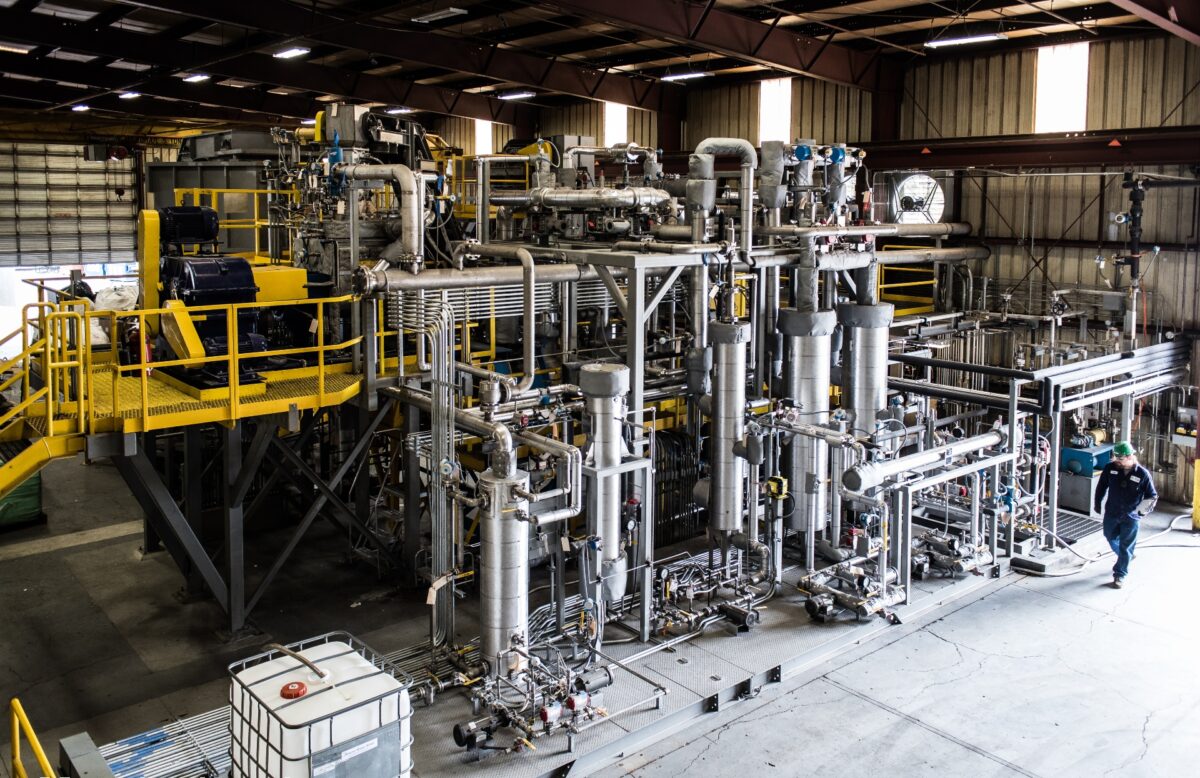
The process, also called advanced recycling, could bring circular sustainability to plastics if implemented on a large scale
Momentum is building for chemical recycling. This technology, also known as advanced recycling, uses various processes to convert plastics waste into chemicals that can be used to produce virgin polymers and other chemicals. Proponents view it as one piece of the puzzle that can keep plastics in use, thus advancing a circular economy.
A few resin producers, among them Eastman Chemical Co., have offered chemical recycling on a targeted basis for years. Eastman has focused on recycling polyester from textiles and other applications. But these technologies are being upgraded to accommodate growing demands for broad plastics recycling.
“Globally we’re seeing consumers, regulators, brand owners and manufacturers of plastics aligned in the view that something needs to be done about plastics waste,” says Tim Stedman, CEO of Agilyx Corp. “We’re at the beginning of a journey with chemical recycling, but I think it’s inevitable that this movement will continue and accelerate.”
Agilyx of Portsmouth, N.H., has been working for more than 16 years to make plastics a renewable resource through advanced recycling. “We view chemical recycling as complementary to mechanical recycling and other initiatives that address sustainability,” says Stedman. “This is a huge global challenge, and we have to leverage everything we can to deal with it.”
The company’s investments in circular pathways work are paying off. “We’ve shown that you can take material that has no home in existing waste systems and turn it back into high-value end products,” says Stedman. “In fact, we’ve shown it is possible to take waste that is low-end and upcycle it to food-grade material. We’re now working to scale these approaches up.”
Creating a Waste Stream
One important challenge is that waste streams are not set up for chemical recycling. Agilyx addresses this through its feedstock management company Cyclyx, a joint venture with ExxonMobil. Cyclyx offers ways to aggregate and preprocess plastics waste for a range of recycling processes while ensuring a reliable supply of feedstock to customers. The company does this by connecting sources of plastics waste that is not being recycled with businesses that want more recycled plastics for their products.
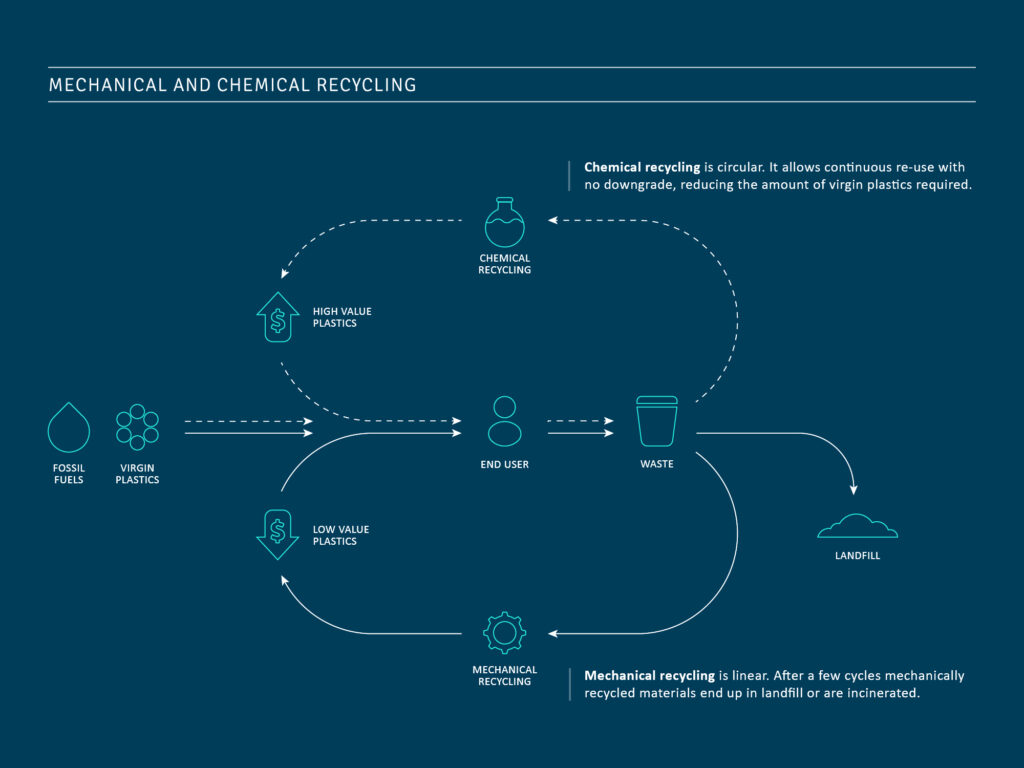
Chemical recycling is a way to continually reuse most plastics by converting waste into virgin monomers. Courtesy of Agilyx
Agilyx also has a pyrolysis-based conversion technology that breaks down a range of waste plastics. The ability to chemically recycle more materials not only increases access to waste but makes the approach economically and environmentally sustainable. “Because our process doesn’t use a catalyst, it can be used on different physical forms and plastics and isn’t affected by high levels of contamination such as food,” says Stedman. “It can also be tuned to produce fuel or a monomer.”
The conversion technology uses electrical heat. Ideally, units based on this process would be incorporated into existing plastics production and recycling plants to maximize synergies between the unit and existing infrastructure, eliminating the need for a separate facility.
Agilyx works with several partners to demonstrate its technology and to accelerate chemical recycling commercially. The company recently announced an agreement to explore the development of a jointly owned advanced recycling facility at AmSty’s styrene production facility in St. James, La. Initially the facility would recycle 50 to 100 tons per day. The facility builds on Agilyx’s advanced recycling technology already in use at the partners’ Regenyx joint venture in Tigard, Ore.
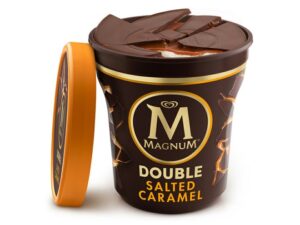
Magnum made more than 7 million ice cream tubs from SABIC’s certified circular polypropylene resin. Courtesy of Unilever
“At Regenyx, we take waste from agriculture and other sources which can be highly contaminated, and together with AmSty, turn this into food-grade polystyrene,” says Stedman. “Advanced recycling is a good fit for polystyrene because it can be converted to its original liquid-form styrene monomer using 40 percent less energy than other polymers.”
Agilyx also works with NextChem, a subsidiary of Maire Tecnimont Group, on development of advanced chemical recycling facilities globally. Under an agreement, NextChem will act as a technology and EPC (engineering, procurement and construction) partner for Agilyx to develop chemical recycling projects for third parties. The first projects include one in Europe and in South America.
New Polymers From Old
Resin producer SABIC is also investing in chemical recycling. “We see chemical recycling as complementary to conventional recycling approaches and key to handling difficult-to-recycle end-of-life plastics like soft or flexible packaging or multilayered products made from different combinations of plastics,” says Mark Vester, global lead for the circular economy. “Currently, these plastics end up in landfills or incineration, which lock them out of reach, destroy future value and, in the case of incineration, risk releasing elevated levels of CO2 into the atmosphere.”
SABIC and Plastic Energy, a chemical recycling company in London, recently announced they are building one of the first commercial units aimed at production of certified circular polymers from used plastics. The unit will be in Geleen, Netherlands, and begin operation in the second half of 2022.
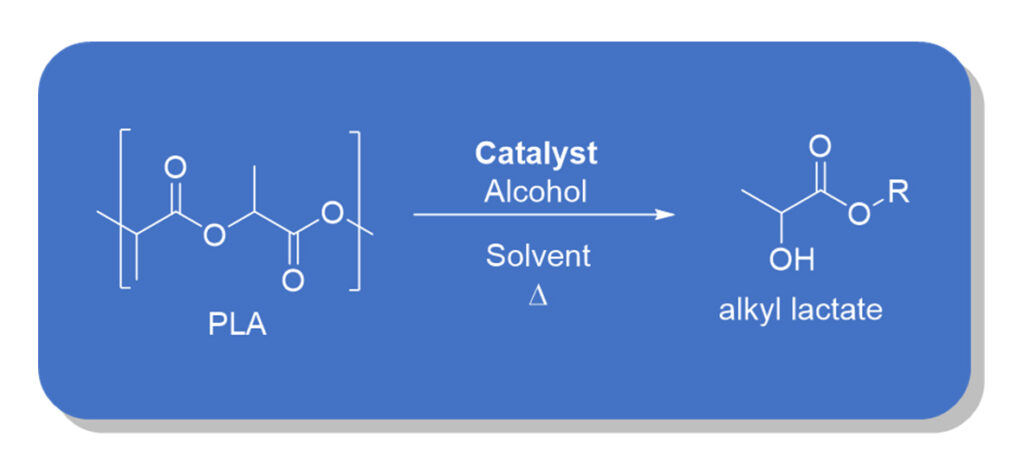
Prof. Mathew Jones is developing ways to break down plant-based PLA and other polyesters using chemical recycling. Although PLA is biodegradable in industrial conditions, there are no commercial ways to recycle it. Courtesy of Mathew Jones
Since 2019, SABIC has worked with Plastic Energy, customers and converters to produce and commercialize certified circular polymers. These are made using Plastic Energy’s advanced recycling technology, which converts waste plastics into pyrolysis oil. SABIC uses the oil in place of fossil fuels to create polymers.
The certified circular polymers have been used in packaging for brands like Unilever, Mars Inc. and Estee Lauder Cos. They are part of SABIC’s Trucircle portfolio, which includes products designed for recyclability, mechanically recycled products, certified circular products from feedstock recycling of plastics and certified renewables products from biobased feedstock.
“A circular value chain for plastics will work differently from our traditionally linear value chain,” says Vester. “Because no single company can transform such a massive and complex industry, it will require partnerships and scale to drive the circular economy forward.”
Toward Circular Use
Vester notes that up to 80 percent of a product’s environmental impact is determined at the design phase. Product design that facilitates recyclability and reuse is thus critical. In addition, mechanical recycling is an established and efficient solution for defined mono-material waste streams like polyethylene terephthalate (PET) and high-density polyethylene. SABIC uses a lifecycle analysis for each product or solution to develop the most appropriate recycling or reuse option.
“Advanced recycling can facilitate the move from a linear to a circular plastics economy by recycling used plastics that would otherwise have been disposed of, but this is complementary to mechanical recycling and reuse options—not instead of,” says Vester. “It will take all these options, together with new ways of working together to create the right conditions, to realize the goal of a fully circular plastics economy.”
Although Vester sees a willingness across the value chain to make large-scale closed-loop commercial packaging a reality, there are challenges to overcome. One is establishing an aligned framework—on a regional or larger level—for waste collection. The range of regulations around waste collection and recycling means there is no consistent starting point.
This is evident in the U.S., where waste collection and recycling are carried out at the municipal level—no single solution has been implemented on a national scale.
“We need to find different ways of working with companies, governments and regulators to bring together the different strands of the value chain and create a framework that provides the right conditions to push the circular economy and advanced recycling forward transparently,” says Vester. “It is also important that advanced recycling be accepted as a recycling technology that counts towards recycling targets such as the ones being set in Europe.”
Recycling Bioplastics
Mathew Jones, professor at the Center for Sustainable & Circular Technologies at the University of Bath, U.K., is developing ways to break down plant-based polylactic acid (PLA) and other polyesters using chemical recycling. Although PLA is biodegradable in industrial conditions, there aren’t commercial ways to recycle it. PLA is used to make biodegradable food packaging and disposable cutlery and cups. “PLA’s market share is increasing, so there will inevitably be a need for PLA recycling strategies,” says Jones. “It is important that we develop the processes for recycling this material before the need is critical.”
Jones’ research group has been working with PLA for years, which means they were able to draw on their experience with characterizing the material when they began working on ways to degrade the bioplastic. The researchers developed catalytic systems for chemical recycling that feature low environmental footprints and aren’t too complex or expensive to make or use. These properties are important to ensure that systems can be successfully scaled up and commercialized.
Their catalysts can be used on other polyesters such as PET. The researchers have shown that monomers isolated from PET can be converted back into the polymer again. “We’ve also shown that our approach works incredibly well for mixed PLA/PET feeds at small-to-medium scales,” says Jones. “We’re working with chemical engineers to scale up our process.”
Jones notes that at larger scales, mixed feeds become a bigger issue. Because the recycling stream not only has different types of polymers but also food waste and other contaminants, a robust chemical recycling process is needed. In addition, monomers made from the process can be challenging to separate. “If you start with a mixed PET/PLA feed then there will be some lactic acid incorporated into the PET monomers, which will affect the repolymerization required to make the PET again,” Jones says. “Because making PET is a polycondensation process, it’s very susceptible to impurities.”
The researchers have carried out preliminary studies using model waste streams containing PLA, polycarbonates and polyesters that show by varying the temperature it is possible to selectively copolymerize one plastic at a time sequentially.
Jones sees chemical recycling as a growing technology. “There might be some plastics where mechanical recycling is the best thing to do, but materials that are difficult to recycle might be better suited to chemical recycling,” he says. “For example, colored PET is quite difficult to recycle mechanically, because it can’t always be separated from other plastics.”