Finally! 3DP of LCP
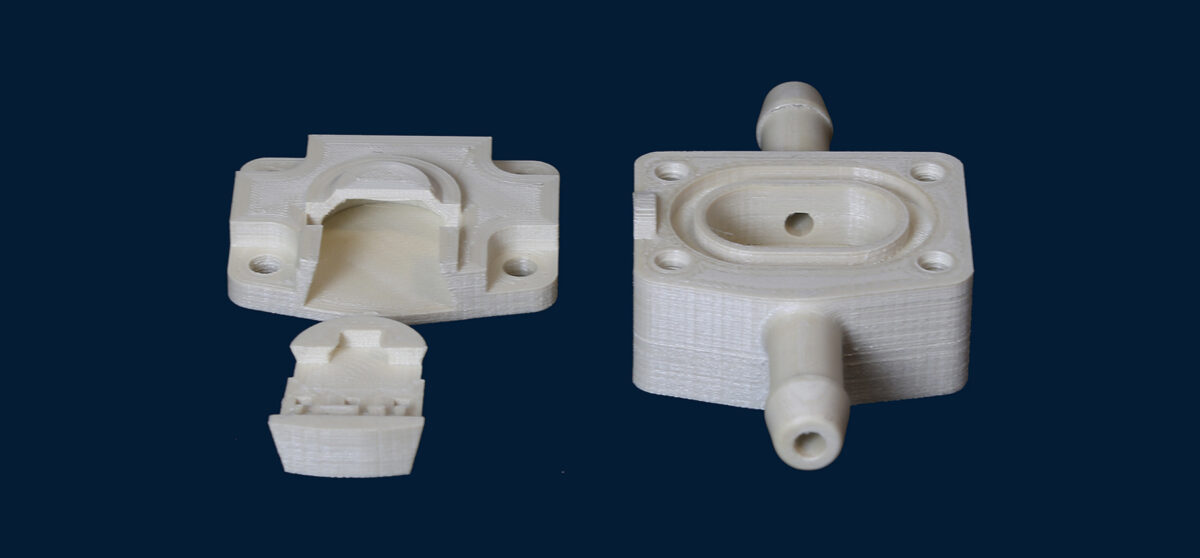
Swiss company develops technology to print liquid crystal polymers
Despite the number of polymers available for 3D printing, a conspicuously absent performance family is liquid crystal polymers (LCPs). That’s changing now that a Swiss startup reports it has solved the technical challenges of 3D printing LCPs and is scaling up initially to offer LCP printing services and ultimately a custom printer/material/software platform based on fused-filament fabrication (FFF) technology to companies wishing to print their own LCP parts.
The company is based in Zürich and called NematX, a clever play on the nematic (mesomorphic) phase of liquid crystals. It’s the brainchild of co-founders Silvan Gantenbein, chief technology officer, and Raphael Heeb, chief executive officer.
The company’s technology was developed over a 5-year period by Gantenbein during his doctoral work at ETH Zürich (Swiss Federal Institute of Technology).
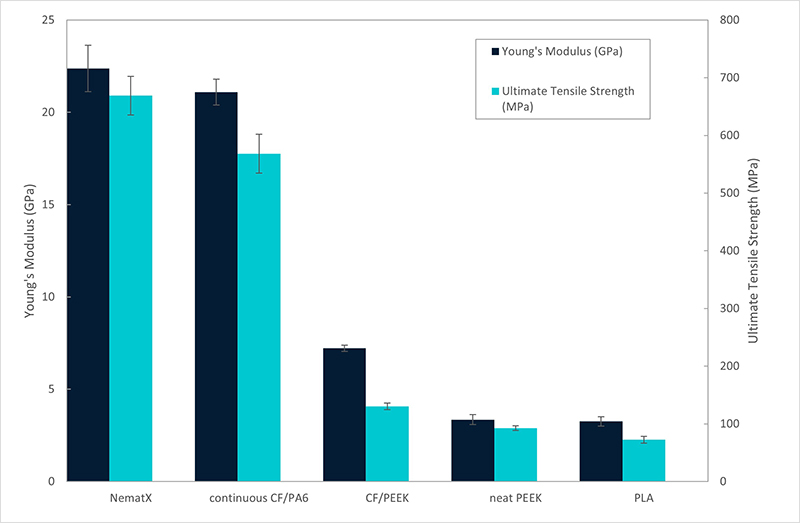
By harnessing the unique properties of LCPs, NematX offers heretofore unachievable stiffness and strength values.
“To successfully print LCPs, you must understand what happens in the material at different length scales,” Gantenbein explains. “While I knew LCP’s anisotropic behavior could be challenging—and, indeed, a major technical challenge I faced was achieving good adhesion between layers in the vertical printing direction—I also understood the potential of self-reinforcement, a property that could be exploited in 3D printing to create parts with tensile stiffness values to 26 GPa and tensile strength to 600 MPa. That motivated me to study the influence of material composition, process parameters and hardware to better control material microstructure and improve printed quality of high-performance polymer parts. While LCPs behave somewhat differently than other thermoplastics, those characteristics are highly attractive in parts, which 3D printing can bring to market faster and at lower cost.”
“Although printing speed is very part-geometry dependent, LCP’s rapid solidification helps us print at faster relative speeds than other performance plastics and their low melt viscosity enables us to print with much higher resolution—25 microns being our production-solution target,” adds Heeb. “By freezing the induced molecular orientation in each layer, polymer products with currently unmatched mechanical and thermal properties and excellent inertness become feasible. Furthermore, LCPs don’t necessarily require a heated chamber the way other high-performance polymers do, simplifying hardware design.”

NematX’s initial market focus is on industrial markets requiring high-performance precision parts in small to medium volumes—electronics, precision mechanics and vacuum/chemical equipment. Longer term, aerospace/aviation, medical devices and automotive may be targets.
NematX recently installed a specialized pilot extrusion line to produce filaments for inhouse development and to print customer parts. In parallel, they’ve developed a proof-of-concept printer (build envelope currently 20 by 20 by 20 centimeters (7.9 by 7.9 by 7.9 inches) wide and 40 by 40 by 40 centimeters (16 by 16 by 16 inches) long and are working with hardware partners to develop commercial equipment. They also have a procedure to recycle printed parts and scrap into new raw material to support the circular economy.