Champion for Change: Sal Monte Redefines Coupling Agents and Catalysts
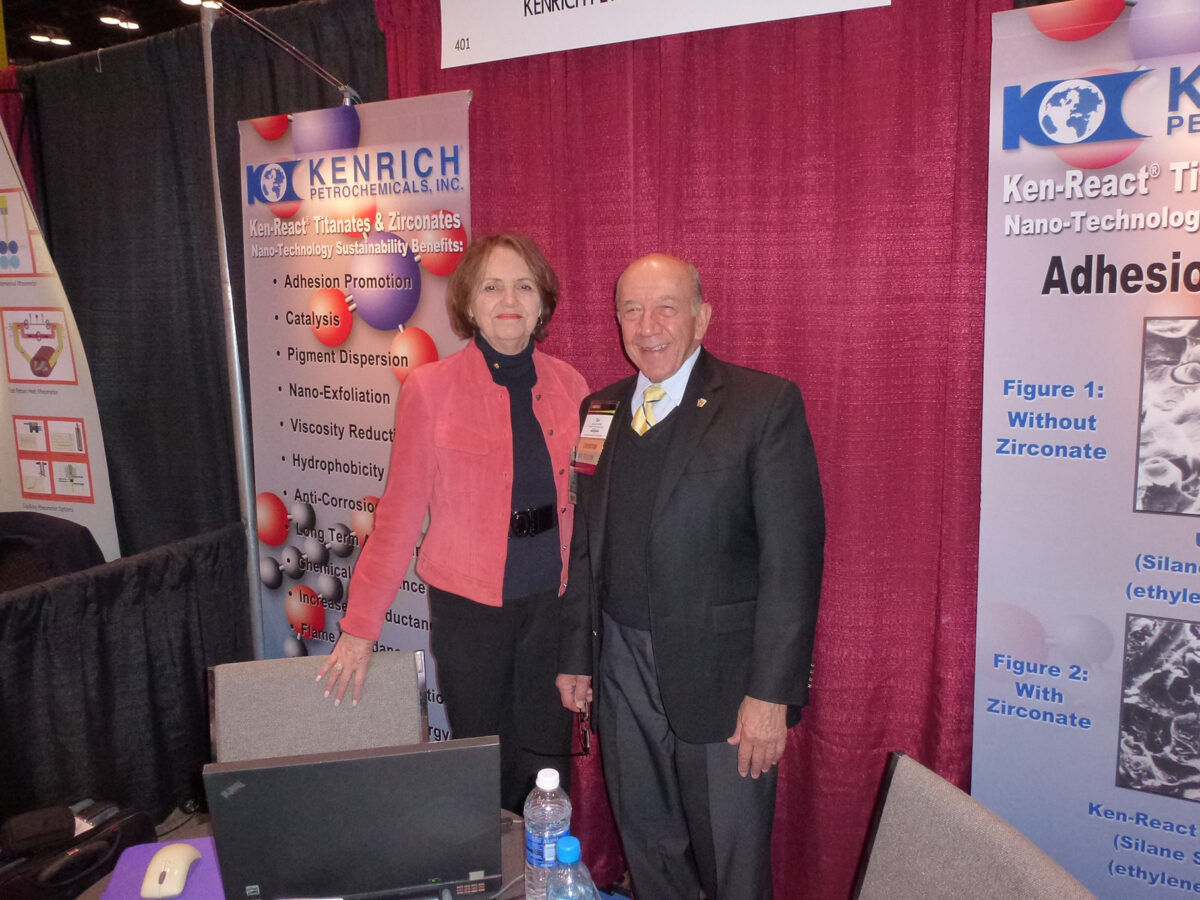
Sal Monte continues to challenge conventional thinking about coupling agents and catalysts
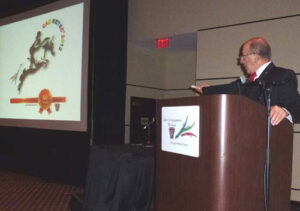
Monte has been a tireless promoter of Ken-React coupling agents and catalysts, detailing their benefits to audiences worldwide.
In 1979, shortly before his 40th birthday, a hard-charging chemical executive named Sal Monte attended a communications development seminar in White Plains, N.Y.
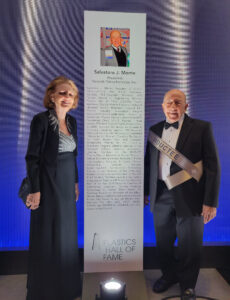
Monte’s standing in the industry was recognized when he was inducted into the Plastics Hall of Fame in 2021. Sal and Erika stand by the list of his accomplishments at the ceremony.
During a break, he discussed his business with one of the speakers, James Cusimano. Monte told Cusimano that he helped his company, Kenrich Petrochemicals of Bayonne, N.J., develop organometallic coupling agents for titanate, zirconate and aluminate technologies. The additives, which also have value as catalysts, improved the properties and processability of numerous materials.
Monte, who was vice president of the company then, believed the coupling agents were suitable for all sorts of materials and could upgrade resin properties in diverse applications. Cusimano probably didn’t follow the technical aspects of the conversation, but he recognized Monte’s enthusiasm for the products.
“Sal Monte,” Cusimano said, “what if I told you your mission in life is to teach people how to use raw materials more efficiently through titanium? Does that mean anything to you?”
For Monte it sounded like affirmation of the work he started in 1973. “The Holy Spirit gave me a message, and that was my job—and I stuck to it,” he says.
Forty-three years later, Monte, now president of Kenrich Petrochemicals, still enthusiastically promotes titanate, zirconate and aluminate technologies wherever he can. Applications for the technologies, meanwhile, continue to grow.
Among his latest targets for the coupling agents and catalysts—tradename Ken-React—is what he terms advanced mechanical recycling of post-consumer plastics. He believes that with the chemistry of the additives mechanical recycling can be as effective at repolymerizing/copolymerizing commingled waste generated by curbside collection as advanced recycling that uses depolymerization processes. Mechanical recycling also does not require huge processing plants and large amounts of energy like advanced recycling does. More on this later.
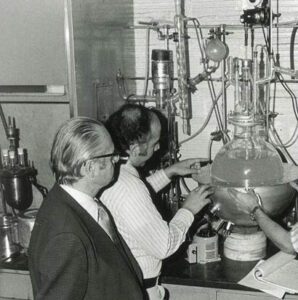
Monte, second from left, helps synthesize titanate at Kenrich in the 1970s.
The Ken-React titanate, zirconate and aluminate coupling agents come as powders, liquids or pellets. According to Kenrich, they form a less than 2-nanometer monomolecular layer on the surface of any organic or inorganic material and chemically bridge non-silane reactive fillers such as calcium carbonate (CaCO3), carbon black, silica, metal oxides and other chemicals with polymers.
The benefits of using the additives are considerable. The website notes that adding just 0.2 to 0.6 phr of titanate to a polymer compound can yield up to 40 percent faster molding cycles and 10 percent lower process temperatures; viscosity can be reduced 20 percent or more; mechanical properties improve; high filler loadings of carbon black, CaCO3, ATH and magnesium hydroxide can be used with no tradeoffs in processability or part flexibility; polymer adhesion to aramids, polyamides, graphite and glass-fiber reinforcements increases significantly; and part smoothness, pigmentation and paintability improve.
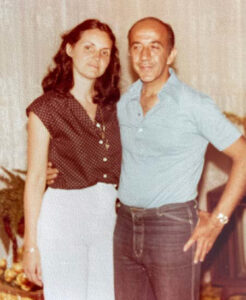
Sal and Erika relax at home in New York City.
At the time, Kenrich Petrochemicals was owned by brothers Oscar and Eric Spiegelhalder. Eric was Monte’s boss and father-in-law. “I married the boss’s daughter, Erika,” says Monte. The two had known each other since they were teenagers. Monte joined the company in April 1966 as vice president with solid credentials. He had an undergraduate degree in civil engineering and was a licensed PE (professional engineer). Once he began working with chemicals at Kenrich, he went back to college and earned a master’s degree in polymer materials at New York University’s Tandon School of Engineering. His wife, Erika, meanwhile, was a director of the company and for many years promoted the Kenrich line with Monte.
In the 1950s, Oscar and Eric, who owned two sucro-chemical companies, purchased the license to a product called Kenflex A, which was developed toward the end of World War II in Socony-Mobil labs in Paulsboro, N.J., by three graduate scientists from the University of Kentucky, who planned to get rich by making use of the bottoms cut from the distillation of gasoline via a formalite condensation polymerization to produce an oligomer plasticizer of polycyclic aromatic hydrocarbons. By 1961, Kenflex A had been approved by DuPont for use in its high-voltage Neoprene and Hypalon wire-and-cable insulation, a major business achievement.
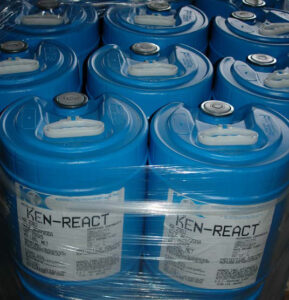
Ready to go: 5-gallon pails of Ken-React coupling agents are packaged for shipping to customers.
In 1973, Monte developed the initial material in the Ken-React line. At first it was intended to be a better way of dispersing zinc oxide in naphthenic oils. He suggested the company make an isostearic acid-based titanate ester to do this. “I knew enough chemistry to be dangerous,” he says. But his idea “worked like gangbusters. I came up with a better coupling/catalyst system for metal oxides.”
The formula was tried on silicas, CaCO3 and other minerals and metal oxides, and worked well in all applications. During the Arab oil crisis of the early 1970s, he says, “Everyone was trying to stretch out polyolefins [in masterbatches] with calcium carbonate [to save money], and the Ken-React formula worked great [for that].” Monte wrote up this finding in an article he submitted to Modern Plastics magazine. MP published it as a feature in December 1974. Once the issue was out, the phones at Kenrich started ringing off the hook, as readers sought more information about the Ken-React material.
From that point on, Sal Monte became the chief salesman—some would say apostle—for titanate, zirconate and aluminate coupling agent and catalyst technologies. Along the way he’s dealt with resistance from companies accustomed to using established coupling agents, notably silanes. “I spent 10 years trying to undo the mindset of silane coupling,” Monte remarks.
Enhanced Recycling
The latest work he’s focusing on is improving the mechanical recycling of plastics waste. Monte believes that the Ken-React coupling agents and catalysts can effectively compatibilize commingled plastics waste from curbside collection.
“The reason why advanced recycling has value is you take material with a known quality and reuse it,” he explains. “But you need a chemical plant to do this, and regulators don’t want chemical plants that consume lots of energy. My concept uses advanced mechanical recycling and titanium aluminum chemistry.”
Mechanical recycling, says Monte, is being done wrong. “They try and mix incompatible plastics from curbside collection. But if they put titanium aluminum additive in the mix, they can improve performance of the recyclate and reuse it in new products.”
Monte says the scrap would need to be in powder or flake form prior to mixing with the titanium and aluminum coupling agent and transferring the blend to a twin-screw extruder for processing and pelletizing. “You need to learn how to prepare a masterbatch in a certain way,” he remarks. “There’s a whole science to mixing that many don’t understand. To work in the melt phase [with coupling agents and catalysts] at the nano level means all the temperature settings, rheology and other parameters are different.” Profile temperatures, for example, might need to be 10 to 20 percent lower than usual to get complete coupling via reactive compounding shear with the Ken-React materials.
Monte has experimented with commingled scrap of PP, high-density PE and PET bottles. They were ground up together with the coupling agent and catalyst added during extrusion. Pellets from the process had higher properties than conventional mechanically recycled plastics. But the experimental process tests cost $25,000 to develop initial data, and the additive has a cost that raises a red flag for potential users who say they can’t even add a penny to the cost of a pound of recyclate. “Right now, recycled material is more expensive than virgin,” Monte notes. “There’d only be a market if there’s a mandate to use recyclate in products.”
The high cost of developing, testing and certifying chemical formulations is a major problem affecting the plastics industry, he says. “It’s very expensive to introduce a chemical today. You can’t just willy-nilly create and innovate. I did one modification on a molecule, and it cost $45,000 to go through the U.S. EPA Pre-Manufacture Notification process. You can’t get approvals in one year in this business. It takes a 3- to 5-year cycle. You need all sorts of approvals.”
It’s a changing world, with product development far more regulated than it used to be. But that hasn’t stopped Monte from working on technologies for various applications. In 2020, he received his 32nd U.S. patent for developing a way of making ordinary Portland cement composites from oil-soaked seawater sand—a hazard of offshore oil spills—by using a nano-level titanate surface modifier.
54 Years in SPE
Meanwhile, Monte has been a member of SPE since 1968, and a leading figure in the plastics industry. The SPE honors he earned include being named a Fellow of the Society, an Honored Service Member, past president of the New Jersey Section, past chairman of the Thermoplastics Materials & Foams Division, and co-founder of the SPE International Foams Conference in 1999.
He is also a member of the Plastics Pioneers Association and of the Plastics Industry Association’s Recycle Subcommittee-Compatibilizers. In 2021, he was inducted into the Plastics Hall of Fame.
Monte has come a long way since joining Kenrich Petrochemicals. He’s made a lasting name for himself in plastics as a tireless advocate for the products that emerged from his idea in 1973 to make an isostearic acid-based titanate-coated zinc oxide.
As the seminar speaker told him so many years ago, his mission in life has indeed been to teach people how to use raw materials more efficiently through titanium, and that doubtless will be one of his most important achievements and his legacy.